PET Bottle Flakes - Lösungen für Verarbeitungsprobleme
Dr. Stephan Gneuß, Gneuß Kunststofftechnik GmbH
Störfaktoren bei der PET - Bottle - Flakes Verarbeitung und Maßnahmen zur Behebung
Bei der Verarbeitung von PET Bottle Flakes kann es zu einer Vielzahl unterschiedlichster Schwierigkeiten kommen, die verursacht werden durch die Vielzahl der Möglichkeiten von Verunreinigungen, als auch Unterschiede in der Bottle Flakes Qualität.
Die Auswirkungen auf die Finalproduktqualität als auch auf den Verarbeitungsprozess sind entsprechend vielfältig.
In den nachfolgenden Aufzeichnungen werden die unterschiedlichen Störfaktoren dargestellt (Abb. 1+2), ihr mögliches Erscheinungsbild aufgezeigt und mögliche Lösungsansätze beschrieben.
Störfaktor: Feuchtigkeit
Ein häufig unterschätzter Störfaktor ist die Feuchtigkeit der Flakes und deren Konstanz bei der Aufschmelzung. Die Feuchtigkeit der Flakes ist eine Variable und schwankt je nach Anlieferungszustand sowie der jeweiligen Luftfeuchtigkeit. In der Regel beträgt die Feuchtigkeit 0,3 - 0,5 % .
Bei der Trocknung der Flakes ist zu unterscheiden zwischen der Oberflächenfeuchte und der Kernfeuchte. Die Oberflächenfeuchte lässt sich verhältnismäßig rasch reduzieren, wobei Luftmenge, Luftgeschwindigkeit, Feuchte der Trockenluft und die Temperatur von Bedeutung sind. Meistens erfolgt dies mit der Materialkristallisation bei ca. 170°C.
Die Kernfeuchte zu reduzieren ist dagegen zeitaufwendiger, da die Transportgeschwindigkeit der Feuchte aus dem PET nicht beliebig beschleunigt werden kann. Kompliziert wird der Trocknungsprozess auch dadurch, dass die Trocknungsgeschwindigkeit mit zunehmender Dicke der Flakes und zunehmendem Kristallisationsgrad abnimmt.
Die Abb. 3 zeigt eine Trockenkurve von PET Granulat mit einer Kantenlänge von 2,6 mm bei einer Temperatur von 175°C im Vakuum (1 mbar).
Der zeitliche und finanzielle Aufwand nimmt mit Reduzierung der restlichen Kernfeuchte deutlich zu und es ist deshalb gut zu überlegen was ist für welches Finalprodukt wirklich erforderlich.
Eine weitere Möglichkeit zum Abbau der Feuchtigkeit ist das Ansetzen eines Vakuums an das aufgeschmolzene PET. Bei Einschneckenextrudern ist der Effekt eher gering, bei Doppelschneckenextrudern dagegen sehr gut und effektvoll. Dieser Unterschied ergibt sich durch die deutlich größere Schmelzeoberfläche in der Vakuumzone bei Doppelschneckenextrudern, wobei hier je nach Fabrikat und Spezifikation auch deutliche Unterschiede möglich sind. Ein zusätzlicher wichtiger Faktor ist natürlich auch die Höhe des Vakuums. Auch hier gilt: Je höher das Vakuum desto besser die Feuchtigkeitsreduzierung desto kostenaufwendiger der Prozess.
Um zum Beispiel die Feuchtigkeit auf 0,005 % zu reduzieren ist ein Vakuum von ca. 2mbar erforderlich. Die Kosten hierfür sind beachtlich.
Zur Redzierung auf eine Feuchtigkeit von 0,03 % ist dagegen bereits ein Vakuum von 20-50mbar ausreichend. Die Kosten und der Bedienaufwand sind deutlich geringer.
Die Frage lautet also: Mit welcher Restfeuchtigkeit kann ein Produkt erfolgreich verarbeitet werden.
Hierzu folgende Hinweise:
- Bei der Stapelfaser genügen ca. 0,03 % Restfeuchte, denn zur Fadenherstellung ist ein IV-Wert von 0,6-0,63 völlig ausreichend. Der hydrolytische Abbau der Schmelzeviskosität ist somit sogar gewünscht und sinnvoll. Gleiches gilt natürlich auch für das Spinnvlies.
- Bei der Herstellung von Granulat zur Produktion von Flaschen ist dagegen der hydrolytische Schmelzabbau nicht gewünscht, denn man braucht für sein Finalprodukt eine möglichst hohe Viskosität. Eine sehr kostenaufwendige Vortrocknung oder ein entsprechendes Vakuum kann man durch einen Trick aber auch hier vermeiden, indem man die Schmelzeverweilzeit auf < 40 Sekunden begrenzt und so den hydrolytischen Abbau minimiert. Bei der Granulierung ist dies grundsätzlich möglich, da der Prozess kurz und überschaubar ist. Wenn der Produktionsprozess kompromisslos entsprechend durchkonzipiert wird, kann dies auch erreicht werden.
- Bei der Herstellung von Folien gilt ähnliches, nur ist hier eine Reduzierung der Verweilzeit auf <40 Sekunden nicht erreichbar. Wir können uns aber vorstellen, dass bei konsequenter Reduzierung der Schmelzeverweilzeit mit entsprechenden Kompromissen bei der Flake-Trocknung erfolgreich gearbeitet werden kann. So könnte man zum Beispiel mit einer guten Reduzierung der Oberflächenfeuchte und einer anschließenden Verarbeitung auf einer Doppelschnecke mit einem Vakuum von ca. 20mbar brillante und auch zugfeste Folien herstellen. Es gibt hier sehr viele gute und erfolg versprechende Lösungsansätze.
Störfaktor: Harte Partikel
Harte Partikel wie zum Beispiel Sand, Glas, Aluminium, Krackprodukte usw. können mit Hilfe einer geeigneten Filtrieranlage der Schmelze entnommen werden. Hierbei ist wichtig, das die Filtration Druck- und Prozesskonstant arbeitet eine kurze Schmelze und Schmutzkuchenverweilzeit aufweist und auch die Möglichkeit einer möglichst feinen Filtration bietet. Auch hier gilt es nicht so fein wie möglich, sonder so fein wie notwendig zu filtrieren. Hierzu einige Orientierungsdaten.
Die gebräuchlichsten Filterfeinheiten
Spinnvliesherstellung | 25-40µ |
Stapelfaserherstellung | 30-60µ |
Flaschenmaterial | 40-60µ |
Flachfolie | 30-60µ |
Monofilamente und Bändchen | 60-100µ |
Da bei der Flakeverarbeitung in der Regel immer eine Schmelzepumpe installiert ist, ist es aus Gründen des Pumpenschutzes unumgänglich das vor der Schmelzepumpe zumindest eine Filtration von 300-500µ erfolgt. Die teilweise großen Unterschiede in der empfohlenen Filterfeinheit basieren auf die teilweise auch großen Unterschiede in der unterschiedlichen Finalproduktqualität, die entsprechend ihres Einsatzgebietes und ihrer Anforderungen auch andere Qualitäten benötigt.
Störfaktor: weiche Partikel
Weiche Partikel sind bei Verwendung der richtigen Filtermittel meistens auch filtrierbar. Dennoch ist es ratsam, den Ursprung dieser Partikel zu ermitteln und wenn möglich in der Vorstufe schon zu beseitigen. So können zum Beispiel ungünstige Extruderspezifikationen Gelpartikel produzieren oder durch gut spezifizierte Aufschmelzzonen und nachfolgende Mischteile Gele zerkleinern oder auflösen. Es gibt also hier zwei Lösungsansätze vorausgesetzt, dass die Gele nicht nach der Filtration produziert werden durch Todecken in der Schmelzepumpe, im statischen Mischer, im Leitungssystem oder der Düse.
Störfaktor: Fremdkunststoffe
Fremdkunststoffe wie Polyethylen, Polypropylen, Polycarbonat usw. sind in den Wasch- und Trennverfahren im Wesentlichen entfernt aber dennoch ist noch ein Restbestandteil in der Regel bei den PET Bottle Flakes noch mit enthalten. Dies ist grundsätzlich auch nicht tragisch, da dieser Anteil nicht störend ist wenn er in der Extrusion gut und homogen mit eingemischt wird. Ein Herausfiltrieren in der Schmelze ist ausgeschlossen.
Erfolgt dagegen nur eine mangelhafte Einmischung und Homogenisierung in der Schmelze, wie dies meistens bei den Einschnecken der Fall ist, können sich Schlieren im Finalprodukt zeigen, oder im Faserbereich Fadenbrüche.
Störfaktor: PVC
PVC lässt sich von den Bottle Flakes nur schwierig im Wasch- und Trennprozess entfernen, da das spezifische Gewicht so ziemlich dem des PET entspricht. Sehr häufig werden schwarze Stippen im Finalprodukt als PVC interpretiert, dies ist - eine sorgfältige Vorbehandlung und Extrusion vorausgesetzt - aber nicht richtig, denn das PVC löst sich im Polyester genauso auf wie alle anderen Kunststoffe, hat nur den zusätzlichen negativen Nebeneffekt, dass es den Polyester gelb- braun je nach Menge farblich verändert. Diese farblichen Veränderungen können schon recht beachtlich sein ( Abb. 5) und ein absolutes Qualitätskriterium darstellen.
Störfaktor: Kleber
Die meisten Kleber mischen sich sehr gut in den Polyester ein, wobei auch hier die Einmischung und Homogenisierung extruderabhängig ist. Manche Kleber können bei mangelhafter Einmischung nicht nur zur verstärkten Schlierenbildung führen, sondern auch so genannte Fischaugen (Gele) bilden. Auch hier hat sich die Doppelschnecke als Problemlöser sehr gut bewährt.
Störfaktor: Holz
Bei Holz gilt grundsätzlich gleiches wie bei "Störfaktor harte Partikel". Es lässt sich recht gut heraus filtrieren. Besonders zu beachten ist bei Holz nur die Tatsache, dass bei zu hoher Temperatur das Holz verbrennt und eine Vielzahl kleiner schwarzer verkohlter Partikel bildet. Für jede Art von Finalprodukt hat dies äußerst negative Auswirkungen. Vermeiden lässt sich dies aber sehr gut, wenn man darauf achtet, dass ein zu hohes ?p im Schmutzkuchen (größer als 20-30 bar) vermieden wird, denn beim Durchströmen der Schmelze durch den Schmutzkuchen erwärmen sich die Holzpartikel derart intensiv, so dass die Gefahr des Verbrennens gegeben ist. Besonders leicht lässt sich dies mit dem druckkonstant arbeitendem RSFgenius beherrschen, da hier diese Werte geregelt eingestellt werden können und zudem auch die Schmutzkuchenverweilzeit über die Regelparameter bestimmt wird. Besser ist die Abtrennung von Holz wegen seiner gegenüber PET wesentlich geringeren Dichte in den Vorstufen der Flakaufbereitung zu bewerkstelligen.
Störfaktor: Gummi
Gummi war in den zurückliegenden Jahren äußerst selten ein Bestandteil von PET Bottle Flakes. Auch er lässt sich wegen des sehr vergleichbaren spezifischen Gewichtes nur schwer von den Polyesterflakes trennen und taucht in jüngster Zeit immer häufiger als Bestandteil der Flakes auf. Grundsätzlich lässt sich Gummi recht gut mit einer Schmelzefiltration entfernen. Je kleiner die Gummipartikel aber sind, desto schwieriger wird es und erfordert den Einsatz von speziellen Siebspezifikationen, da sonst die Rückreinigung der Filterelemente kaum möglich ist und somit ein Problem darstellten (Abb.6). Auch hier sind die geregelte Druckkonstanz und eine nicht zu hohes ?p im Schmutzkuchen ( < 20-30 bar ?p je nach Gummipartikelgröße) sehr hilfreich.
Störfaktor: Schwankungen aus dem Extrusionsprozess
Maß- und Toleranzschwankungen am Finalprodukt als auch Veränderungen in der Zugfestigkeit oder in der Materialbrillanz haben in der Regel ihre Ursache im Verarbeitungsprozess. Der gesamte Verarbeitungsprozess setzt sich aus verschiedenen Anlagenkomponenten zusammen, welche sich prozesstechnisch auswirken, wenn sie instabil und fehlerhaft arbeiten. Hierzu einige Beispiele.
- Schwankungen in der Materialfeuchtigkeit führen beim Einschneckenextruder auch zu Schwankungen in der Schmelzeviskosität und allen sich daraus ergebenden negativen Eigenschaften.
- Schwankungen oder Veränderungen in der Vakuumstation bei Doppelschnecken führen zu Veränderung der Schmelzeviskosität sowie der Brillanz im Finalprodukt.
- Schmelzefiltration: Hier führen Veränderungen im Druckverbrauch zu Veränderungen der Schmelzeviskosität (Abb. 7). Todecken und lange Verweilzeiten führen zu Krackprodukten, Gelen und thermisch geschädigten Schmelzen. Hinzu kommt, dass fast alle rückspülenden Schmelzefilter große Schwankungen in der Durchsatzkonstanz haben mit entsprechend gravierenden Auswirkungen auf die verschiedensten Faktoren der Finalproduktqualität.
- Schmelzepumpen, Todecken und mangelhafte Lagerschmierung können Fischaugen, Krackprodukte und sonstige Störungen verursachen. Hohe Schmelzverweilzeiten durch zu große Materialtaschen wirken sich ebenfalls negativ auf die Schmelzqualität aus.
Welche Produkte und Leistungen liefert Gneuß zur Verbesserung des Verarbeitungsprozesses von PET Bottle Flakes?
1. Schmelzefilter RSFgenius
Dieser Schmelzefilter arbeitet vollautomatisch bis zu Filterfeinheiten von 3µ. In der Polyesterverarbeitung sind Durchsatzleistungen bis zu 16t pro Stunde möglich, seine druck- und prozesskonstante Arbeitsweise bei extrem geringen Verweilzeiten von Schmelze und Schmutzkuchen garantieren keinerlei negativen Einfluss auf den gesamten Verarbeitungsprozess. Das gilt insbesondere für den eingangs erwähnten Einfluss der Verweilzeit der Schmelze auf deren hydrolytischen Abbau. Die sehr geringe Verweilzeit von nur wenigen Sekunden im Filterapparat erlaubt eine erfolgreiche Minimierung der Gesamtverweildauer der Schmelze im Prozess und damit eine wesentliche Reduzierung des hydrolytischen Abbaues.
2. Schmelzefilter und Schmelzepumpenkombination
Mit namhaften Pumpenherstellern hat Gneuß eine Filterpumpenkombination entwickelt, welche eine Schmelzeverweilzeit von < 20 Sekunden garantiert. Höchste Anforderungen an Schmelzereinheit und maximal möglicher Schmelzeviskosität können damit gewährleistet werden.
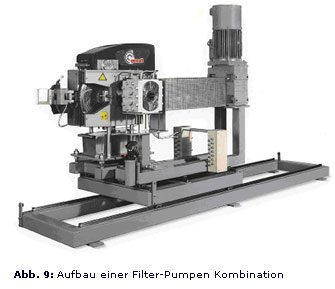 |
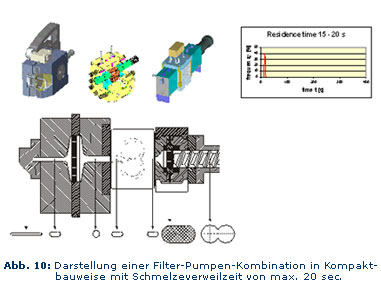 |
3. Online Schmelzeviskosimeter
Störungen im Verarbeitungsprozess als auch in der Materialkonstanz können damit umgehend erfasst werden. Die Möglichkeit des sofortigen Reagierens oder auch die Schaffung zusätzlicher Regelkreise zur Behebung des Problems sind damit gewährleistet. Das Viskosimeter zeichnet sich durch seine todzonenfreie kompakte Bauweise aus, sowie sein sehr günstiges Preis- Leistungsverhältnis.
4. Schmelzedrucksensoren, beheizbar
Sehr häufig werden die Drucksensoren bei der Entnahme einer abgekühlten Anlage oder auch beim Abkühlungsprozess selbst zerstört oder in Ihrer Messgenauigkeit stark beeinträchtigt. Sind die Drucksensoren in einem Regelkreis eingebunden, sind die Auswirkungen auf den Verarbeitungsprozess elementar und sehr kostspielig. Um dies zu verhindern hat Gneuß einen Drucksensor entwickelt, welcher beim Erkalten der Anlage die erforderliche Schmelzetemperatur beibehält und somit die Beschädigung verhindert.
Fazit:
Seit über 15 Jahren hat Gneuß Kunststofftechnik mit namhaften Herstellern und Verarbeitern von Polyester intensive Entwicklung und Forschungsarbeit geleistet und damit heute erprobte Produkte auf dem Markt, welche in der Polyesterverarbeitung weltmarktführend sind. Hierzu zählen selbstverständlich auch außerordentliche Leistungen in Qualität und Service.
Gneuß Kunststofftechnik GmbH
Mönichhusen 42
32549 Bad Oeynhausen, Deutschland
Tel.: +49 (0) 5731 5307-0 Fax: +49 (0) 5731 5307-77
Internet: www.gneuss.de |