Qualitätskonstanz von Folien und Bändchen durch Vollautomatische Filtration
Dr.-Ing. Axel Hannemann, Gneuß Kunststofftechnik GmbH
Bei der Herstellung von Folien und Bändchen nehmen eine gleich bleibend hohe Qualität und eine ökonomische Produktion eine immer größer werdende Bedeutung ein, um im harten Wettbewerb des globalen Marktes bestehen zu können. Ganz besonders trifft dies auf den Verpackungssektor zu. Hinzu kommen immer speziellere Anforderungen, die vom Markt an die Folie gestellt werden.
Dies führte zu immer ausgereifteren und komplexeren Anlagentechniken, welche die optimale Ausnutzung der Polymereigenschaften und Maßhaltigkeit gewährleisten
Der Preis einer Folie wird im wesentlichen durch den Materialpreis und weniger durch die Investition der Anlage bestimmt, solange eine voll ausgelastete Anlage vorgesetzt werden kann. Produktionsunterbrechungen führen unweigerlich zu einer Verringerung der Marge.
"Rohstoffbedingte Kostensteigerungen in der jetzigen
Größenordnung lassen sich - wenn überhaupt - im Endproduktpreis
nur erheblich zeitverzögert weitergeben." (Zitat KI Kunststoffinformationen Nr. 1593, Jg. 32)
Neben den Anlagenkomponenten wie Extruder, Werkzeug und Wicklung, die speziell auf das zu fertigende Produkt abgestimmt werden, kommt dem eingesetzten Filter eine zentrale Rolle zu. Bei der richtigen Wahl trägt es nicht nur entscheidend zur Erfüllung der sich ständig steigenden verfahrenstechnischen Anforderungen bei, sondern führt auch zu einer erheblich wirtschaftlicheren Produktion.
Diskontinuierliche Sicherheitsfiltration:
Beim Einsatz von absolut reinem, neuwertigem Polymer wird in der Regel ein sehr grobes Sieb eingesetzt, um größere Partikel vom nachfolgenden Extrusionsprozess fernzuhalten. Die Siebfeinheit ist nicht selten gröber als 300 µm, um Pumpe und Werkzeug vor Beschädigungen und eventuellen Verstopfungen, die einen langen Anlagenstop bedeuten würden, zu vermeiden. Bei diesen Systemen genügt eine Siebstandzeit, bis die Anlage aus Wartungsgründen ohnehin gestoppt werden muss.
Die hierfür auf dem Markt erhältlichen Systeme sind ähnlich im Aufbau: ein Schieber oder ein Bolzen mit der Aufnahmemöglichkeit für zwei Siebe befindet sich in einem Metallgehäuse. Üblicherweise wird mit Hilfe eines Drucksensors der Flusswiderstand der Siebe und damit der Verschmutzungsgrad gemessen. Sobald ein eingestellter Sollwert erreicht ist, muss das Sieb manuell oder hydraulisch gewechselt werden. Hierzu muss der Durchsatz der Anlage reduziert oder gar gestoppt werden, auf jeden Fall ist mit einer Markierung / Abriss der Folie zu rechnen.
Diskontinuierlicher Siebwechsler HSprimus
Diese Variante des Siebwechslers ist also nur dann einzusetzen, wenn das Siebwechselintervall so lange ist, dass man diesen Wechsel dann auslösen kann, wenn ohnehin ein Stillstand der Anlage zwecks Wartung ansteht.
Ein Einsatz von Regenerat ist deshalb aus wirtschaftlichen Gründen nicht realisierbar, Kostenreduktion durch Recyclingware anstelle von teurem Neupolymer ausgeschlossen.
Eine Weiterentwicklung dieses diskontinuierlichen Filtrationssystems ist der sogenannte Doppelschieber- oder Doppelkolbenwechsler. Hier wird der Schmelzestrom in zwei Ströme aufgeteilt, die dann jeweils durch ein Sieb filtriert werden. Grundsätzlich muss dann während des Wechselns der Extruder nicht gestoppt werden, durch den Verschluss eines Stromes und dem damit verbundenen Druckanstieg beim Wechseln eines Siebes kommt es durch das Strömen durch die verbleibende Kavität jedoch zu massiven Produktionsstörungen und massiven Qualitätseinbruch. Es werden über einen längeren Zeitraum ( ca. ¼ - ½ Stunde) Stippen mit eingeschleppt und nicht selten kommt es trotzdem zu einem Abriss der produzierten Folie, so dass der Begriff kontinuierlicher Siebwechsler für dieses Bauart irreführend ist, da zumindest die Qualität des Produktes nicht gleichbleibend sein kann.
Vollautomatisches, prozesskonstantes Filtriersystem "RSFgenius"
Das von der Firma Gneuß Kunststofftechnik GmbH entwickelte und seit Jahren in der Praxis erprobte, druck- und prozesskonstante sowie vollautomatisch arbeitende Filtriersystem RSFgenius, zeichnet sich speziell in dieser Branche als Garant für gleichbleibende Folienqualität auf höchstem Niveau ab.
Hauptbaugruppen des RSFgenius
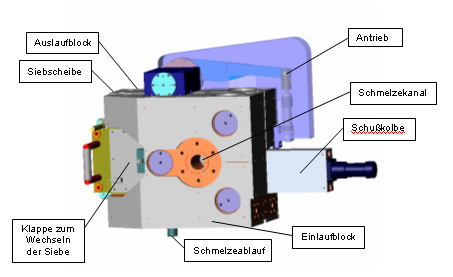
Der RSFgenius besteht im wesentlichen aus drei Teilen, einem Einlauf-, einem Auslaufblock und einer sich dazwischen drehenden Siebscheibe. Die Dichtung dieser drei Teile erfolgt durch sehr enge Spalte und sehr harte sowie ebene Oberflächen. Durch diese Bauweise ist gewährleistet, dass sämtliche schmelzeberührenden Bauteile vollständig von Umwelteinflüssen wie z.B. Sauerstoff getrennt sind. Auf der Scheibe sind ringförmig mehrere Siebelemente angeordnet, die sich durch den Schmelzekanal bewegen. Beim Durchströmen der Siebfläche mit Kunststoffschmelze lagern sich die Partikeln darauf ab, der Differenzdruck steigt leicht an. Die Steuerung reagiert auf diesen Druckanstieg und lässt die Siebscheibe dann etwa 1° weitertakten. Dadurch wird kontinuierlich verschmutzte Siebfläche aus dem Schmelzekanal heraus und frische Siebfläche in den Kanal hineinbewegt. Durch diese Betriebsweise arbeitet das Filtriersystem prozess- und druckkonstant. Die Variation der Druckdifferenz über dem Filter ( p) beträgt max. 2 bar.
Die Reinigung der verschmutzten Filterfläche erfolgt kurz vor dem Wiedereintritt in den Schmelzekanal. Dabei wird der Schmutzkuchen durch eine Hochdrucksegmentrückspülung abgereinigt. Hierzu wird bereits gefilterte Schmelze aus dem Auslaufblock in einen hydraulisch angetriebenen Schusstopf "geladen" und danach unter hohem Druck von hinten durch das sich in der Siebscheibe befindliche Sieb in den Einlaufblock mit ca. 30 - 80 bar geschossen, von wo sie definiert abgeführt wird. Dieser Reinigungsdruck wird auf einen zu bestimmenden Druck konstant geregelt. Es wird jeweils nur ein kleines Segment (ca. 1% der Siebfläche) freigeschossen, so dass jedes Mal ein definiert hoher Impuls zur Reinigung zur Verfügung steht. Durch die Steuerung der Hydraulik ist sowohl der Weg des Schusskolbens (=Schmelzemenge zur Abreinigung) als auch die Geschwindigkeit (=Intensität der Abreinigung) frei justierbar, so dass für jede Anwendung eine optimal geringe Menge für die Abreinigung verfügbar ist. Durch diese Arbeitsweise werden die Siebe annähernd zu 100% gereinigt und können je nach Filterfeinheit bis zu 200 mal wiederverwendet werden.
Somit ist eine zu jeder Zeit eine gleichbleibend hohe Folienqualität gewährleistet, egal ob sich das Filtrationssystem in Wartestellung befindet, taktet, rückspült oder die Siebe gewechselt werden.
Erfahrungsbericht:
Die folgenden Aufzeichnungen sind aus einem Produktionsbetrieb entnommen, der gereckte Folie (Folienbändchen) aus Polypropylen herstellt. Die Dicke der Folie nach Verlassen der Breitschlitzdüse beträgt 335 µm, später wird diese auf eine Enddicke von 150 µm verstreckt.
Zu Beginn der Extrusionslinie steht ein 90 mm Einschneckenextruder, der direkt an das Filtriersystem RSFgenius75 (aktive Filterfläche 90 cm²) mit anschließender Breitschlitzdüse adaptiert ist. Nach der Flachdüse ist das Walz- und Reckwerk angeordnet.
Der Durchsatz der Anlage beträgt 330 kg/h und das in das Filtrationssystem eingebrachte Siebpaket hat eine Filterfeinheit von 40 µm.
Die Folie wird kontinuierlich mit einem Dickenmessgerät online überwacht.
Im Aufzeichnungsprotokoll ist auf der Abszisse die relative Rollenbreite in Prozent aufgetragen, auf der ersten Ordinate die absolute Foliendicke in µm. Auf der zweiten Ordinate ist die maximale relative Abweichung bezogen auf den Sollwert von 335 µm abgetragen.
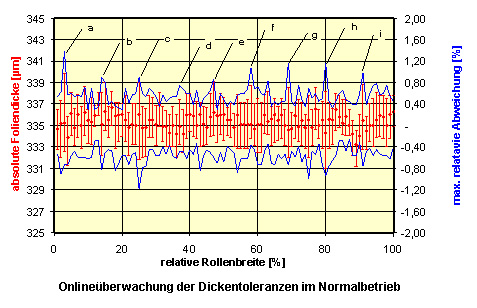
Das Messgerät misst fortlaufend die absolute Dicke der Folie, alle 18s werden statistische Daten wie Mittelwert und Varianz auf einem Bildschirm ausgegeben und in einem Rechner archiviert. Der jeweilige Mittelwert ist durch eine Raute und die absolute Abweichung durch senkrechten Streifen rot dargestellt. Blau dargestellt ist der Quotient aus der maximalen Abweichung und dem Sollwert von 335 µm, die sogenannte maximale relative Abweichung eines Messintervalls von 18s.
Die Querbewegung des Sensors ist so bestimmt, dass die gesamte Breite der Folie in 100 Messabschnitte eingeteilt ist. Somit wird die Breite der Folie einmal in 1800 s = 30 min erfasst.
Die Grundtaktzeit des Filtriersystems, also die Zeit, in der der Filter ein kleines Stück weitertaktet und damit verbunden eine Siebsegmentreinigung durchführt, wurde mit 180 s eingestellt. Diese Betriebsweise wurde gewählt, um eine eindeutige Zuordnung der Takte auf die Foliendicke festzustellen. Theoretisch muss sich also eine Abweichung alle 180 s oder alle 10 Messintervalle ergeben. Diese Werte sind wegen der hohen Auflösung des oberen Diagramms zu erkennen und sind mit a - i gekennzeichnet. Die absolute Abweichung der Foliendicke beträgt maximal ± 5 µm, durchschnittlich ± 3,0 µm, was eine relative Abweichung von ± 1,5 bzw. ± 0,9 % ausmacht. Verglichen mit der normalen Abweichung von etwa ± 0,6 % durch den restlichen Extrusionsprozess ist dieser Wert nur minimal erhöht. Wenn man nun bedenkt, dass diese Folie ohne Schmelzepumpe produziert wird, kann man diese Werte als exzellent bezeichnen.
Um den Einfluss des Filters auf die produzierte Folie zu maximieren, wurde ein weiterer Versuch gefahren. Es wurden bei laufendem Betrieb die Siebelemente gewechselt, also die größtmögliche Störung, die der Filter hervorrufen kann. Der Siebwechsel, der etwa einmal in 3 Monaten fällig wird, dauert ca. 10 min, wobei danach keinerlei Bedieneraufmerksamkeit bis zum nächsten Wechsel notwendig ist. Die Aufzeichnung der Foliendicke während dieser Zeit ist auf der nächsten Abbildung zu erkennen.
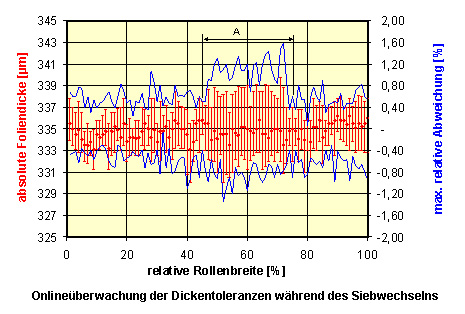
Man kann auch hier aufgrund der hohen Auflösung des Diagramms die Siebelementwechselzeit (A) deutlich erkennen, die Foliendicke wird hier maximal 5 µm erhöht, dies entspricht einer relativen Abweichung von weniger als 1,6 %.
Die Qualität der Folie ist somit auch in dieser Zeit als absolut hochwertig zu bezeichnen.
Somit ist also eine gleichbleibend hohe Qualität der produzierten Bändchen auch bei Filterelementwechsel gewährleistet.
Fazit:
Für die Produktion von hochwertigen Folien ist ein störungsfreier Betrieb mit gleichbleibenden Produktionsbedingungen über lange Zeiträume unerlässlich, um wirtschaftlich effizient auf dem Markt bestehen zu können.
Hierzu ist unter anderem ein Filtrationssystem notwendig, welches diese konstanten Bedingungen gewährleisten kann.
Das Filtriersystem RSFgenius von Gneuß erfüllt die Anforderungen uneingeschränkt und ist somit die ideale Filtrationslösung für die wirtschaftliche Herstellung von Folien mit höchsten Qualitätsansprüchen.
Dies gilt natürlich nicht nur bei der Herstellung von Bändchen, wie im beschriebenen Beispiel. Vielmehr lässt sich dies auch auf alle Arten von Folien, einschließlich axial verstreckten Folien als auch Beschichtung übertragen. Vor allem bei sehr dünnen Folien und der Inline - Technologie kommt die vollautomatische, druck- und prozesskonstante Arbeitsweise zum Tragen.
Die gerade in der letzten Zeit zunehmende Verarbeitung von "Bottle Flakes" zur Reduzierung der Materialeinsatzkosteen erfordert eine erhöhte und verbesserte Filtration. Sie lässt sich mit dem RSFgenius ohne Kompromisse realisieren. Die Amortisationszeit ist dann natürlich besonders kurz.
RSFgenius175 mit Hydraulik und Steuerung
(Einsatzmöglichkeit z.B. für PET Flachfolie aus 100 % Bottle Flakes bei einem Durchsatz von 1200 kg/h und einer Filterfeinheit von 40 µm)
Gneuß Kunststofftechnik GmbH
Mönichhusen 42
32549 Bad Oeynhausen, Deutschland
Tel.: +49 (0) 5731 5307-0 Fax: +49 (0) 5731 5307-77
Internet: www.gneuss.de |