Der Widerspenstigen Zähmung - Verhakte Angussspinnen aufbereiten
Dipl.-Ing. Gunter Schippers, NUGA AG Kunststoffschneidmühlen, Balgach/Schweiz
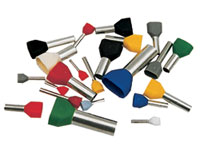 Die Zoller+Fröhlich GmbH stellt in Wangen im Allgäu seit 1968 Aderendhülsen (Bild 1, rechts) für Leiterkabel von 0,14-150 mm² her, die weltweit von Kunden aus der Elektroindustrie, dem Anlagenbau u.a. eingesetzt werden. Die metallischen "Adernaufnehmer" werden dabei in Spritzgießmaschinen mit einem Kunststoffkragen umspritzt ("Einlegespritzgießen"). Sie werden in unterschiedlichen Formen und Ausführungen und in einer Vielzahl von Farben produziert. Das Gewicht und das Volumen der entstehenden Angussspinnen übersteigen dabei um das Mehrfache das Gewicht und das Volumen der produzierten Teile. Eine wirtschaftliche Aufbereitung und anschließende Wiederverwendung des thermoplastischen Kunststoffs ist deshalb aufgrund der Materialkosten unumgänglich.
Verhakte Angussspinnen vereinzeln
Bei der Gestaltung der Formnester und der Angusskanäle in den Spritzgießformen wird besonders darauf geachtet, dass Fließlänge und effektiver Druck überall gleich sind, damit alle Teile von gleicher Qualität sind. Daraus ergibt sich beispielsweise eine kreisrunde Form der Angussspinnen, mit produktionsbedingt gleichmäßig angeordneten spitzen Abreißpunkten. Die Aderendhülsen werden beim Entformen von den Angussspinnen abgetrennt. Diese werden separat ausgeworfen und nach Farben getrennt direkt an den Spritzgießmaschinen in Gitterboxen gesammelt. Hier entsteht nun ein Haufwerk ineinander verhakter und schwer wieder zu entwirrender Angussspinnen. Ein manuelles Auflösen dieses Materialgewirrs ist sehr kostenintensiv und aufgrund der anfallenden Mengen nicht realisierbar. Die speziell für diese Aufgabenstellung ausgelegte Aufbereitungsanlage der NUGA AG aus Balgach/Schweiz, die aus einem sogenannten "Vereinzeler" und aus einer Schneidmühle vom Typ CentriCut 22 besteht (Bild 2, rechts), automatisiert diesen Prozess.
Über eine Kippvorrichtung für die Gitterboxen wird das Haufwerk der ineinander verhakten Angussspinnen dem oben offenen Aufnahmetrichter des Vereinzelers zugeführt, wobei es aufgrund der Gewichtskraft gegen den Trichterboden gedrückt wird. Im schräg ansteigenden Boden des Trichters sind in gleichmäßigem Abstand vier Förderketten mit Vereinzelungszähnen integriert, die unterhalb des Trichters umlaufen. Diese Vereinzelungszähne greifen in das Haufwerk ein, ziehen es auseinander und transportieren die nun vereinzelten Angussspinnen (Bild 3, unten) in die Schneidmühle.
Der Vorgang der Entwirrung wird durch drei zusätzliche Abstreif- bzw. Vereinzelungsketten unterstützt, die in die vordere Trichterwand integriert sind und vertikal von unten nach oben laufen. Deren Vereinzelungszähne, die nach oben laufend in der Gehäusewand verschwinden, greifen ebenfalls in das Materialgewirr ein und unterstützen durch Mitnahme von Angussspinnen den Vorgang der Entwirrung.
Der Antrieb der Förder- und der Abstreif- bzw. Vereinzelungsketten, die in der Regel mit gleicher Geschwindigkeit laufen, erfolgt über einen Elektromotor mit 2,5 kW Antriebsleistung. Die Geschwindigkeit ist optional mittels eines Frequenzumformers stufenlos einstellbar, so dass je nach Form und Beschaffenheit der Angussspinnen bzw. der Leistungsfähigkeit der nachgeordneten Schneidmühle eine optimale Fördergeschwindigkeit eingestellt werden kann.
Die gesamte Anlage wird lastabhängig gesteuert, um ein Überfüllen der Schneidmühle durch den Vereinzeler zu verhindern. Optional kann zwischen Vereinzeler und Schneidmühle eine Metalldetektion bzw. Metallseparation integriert werden, um metallische Fremdkörper zu entdecken bzw. auszuschleußen.
Zerkleinerung der Angussspinnen
Über einen Einfüllschacht werden die vereinzelten Angussspinnen nun der Schneidmühle CentriCut 22 zugeführt. Über eine horizontal angeordnete Schnecke wird der Materialstrom dem Rotor zwangsweise axial zugeführt.
Die vom sich drehenden Rotor erzeugte Zentrifugalkraft schleudert das zu zerkleinernde Material durch den offenen Rotor gegen die vom Sieb und den Statormessern gebildete Mahlkammerwand, die einen über 360° komplett geschlossenen Mahlraum umschließt (Bild 4, rechts). Dort wird es zwischen den Rotor- und Statormessern zu einem scharf geschnittenen und staubarmen Mahlgut zerkleinert. Der Rotor ist offen, wodurch konstruktionsbedingt geringe Massen zu bewegen sind, was einen niedrigen Energieverbrauch zur Folge hat.
Durch zwei um den Mahlraum angeordnete Lochsiebe wird das sortenreine Mahlgut nun durch eine integrierte, kraftvolle Absaugung schnell ausgetragen, nachfolgend entstaubt und anschließend in der Produktion der Neuware zudosiert. Die sehr kurze Verweilzeit des zu zerkleinernden Materials in der Maschine führt ebenfalls zu einem niedrigen spezifischen Energieverbrauch, zu einem geringen Messerverschleiß und letztlich zu einem extrem hohen Durchsatz.
Eine elektronische und lastabhängig geregelte Steuerung zwischen Rotor und Schneckenwelle verhindert ein Überfüllen des Mahlraumes sowie einen Materialstau am Sieb und ermöglicht in der Regel auch bei Materialrückständen ein Anfahren aus dem Stillstand. Der Durchsatz der CentriCut 22 liegt bei ca. 100-200 kg/h. Die Antriebsleistung beträgt dabei nur 6,5 kW. Die innovative Materialzuführung und die Rotorgestaltung ermöglicht eine kompakte und energiesparende Bauweise der Schneidmühle. Der Rotordurchmesser beträgt 220 mm und die Rotorbreite 160 mm.
CentriCut - Superschnelle Reinigung macht häufige und schnelle Farbwechsel möglich
Die integrierte Absaugung ermöglicht einerseits einen schnellstmöglichen Austrag des Mahlgutes und andererseits eine sehr schnelle Reinigung der Schneidmühle. Das ist insbesondere bei häufigen Farb- bzw. Materialwechseln von Vorteil und ermöglicht zudem eine gleichmäßige Auslastung der Anlage.
Das Öffnen des Mahlraumes erfolgt werkzeuglos über seitlich ausschwenkbare Siebkörbe, wodurch auch ein schneller Siebwechsel möglich ist, beispielsweise bei Änderung der gewünschten Korngröße. Die Maschinen sind mit einem komplett integriertem Sicherheits- und Schallschutzgehäuse ausgestattet.
Heinrich Kemler, Fertigungsleiter Mechanik bei Zoller+Fröhlich: "Das sehr ungünstige Verhältnis vom Gewicht unserer produzierten Teile und der anfallenden Angussspinnen erfordert aus Kostengründen unbedingt deren wirtschaftliche Aufbereitung. Die große Vielfalt an unterschiedlichen Farben erfordert weiterhin eine flexible, schnelle und sichere Handhabung der Materialströme. Insbesondere bei der Vereinzelung hat die NUGA AG quasi in Pionierarbeit die gestellte Aufgabenstellung umgesetzt. Die Maschine erfüllt hierbei auf hervorragende Art und Weise die schwierige Aufgabe der Vereinzelung von verhakten Angussspinnen aus Haufwerken. Die superschnelle und sichere Reinigung der Schneidmühle erfüllt unsere Erwartungen und macht die häufig anfallenden Farbwechsel einfach handhabbar."
Nuga Systems AG
Haupstrasse 64a
9436 Balgach, Schweiz
Tel.: +41 71 720 00 40 Fax: +41 71 720 00 45
Internet: www.nuga-systems.ch |