Granulieranlagen für das Kunststoffrecycling - neue technische und wirtschaftliche Ansätze
Dr. Horst Müller, Dipl.-Ing. Harald Zang, Rieter Automatik GmbH
Bei vielen Fragestellungen des Recyclings von Kunststoffen ist das Granulieren, nach vielen anderen Zwischenschritten, einer der letzten Arbeitsgänge. Dadurch wird dem Recyclingprodukt sozusagen "der letzte Schliff" gegeben, d.h. es wird für die nachfolgende Verarbeitung zu neuen Produkten in die ideale Ausgangsform gebracht.
Grundsätzlich stehen für das Granulieren eine Vielzahl von Verfahrensvarianten (Tabelle 1) zur Verfügung. Bezüglich der Eigenschaften des Eingangsmaterials bzw. des herzustellenden Produkts, aber auch im Hinblick auf die Wirtschaftlichkeit sind an solche Granulierverfahren bei Recyclinganwendungen besondere Anforderungen zu stellen. Im Folgenden werden drei exemplarisch ausgewählte Verfahren bzw. Anlagentypen analysiert und Kriterien für die Auswahl der optimalen Technik dargestellt.
Tabelle 1: Übersicht der Granulierverfahren und -anlagen
Konventionelle Stranggranulierung
Bei der konventionellen Stranggranulierung werden im Extruder erzeugte Stränge in einem Wasserbad abgekühlt. Das am Polymerstrang anhaftende Kühlwasser wird mittels einer Strangabsaugung entfernt. Im Stranggranulator werden die Stränge zwischen einer feststehenden Messerleiste und dem sich drehenden Schneidrotor zu Granulat geschnitten.
WSG-Anlagen sind die konventionellen Stranggranulieranlagen von Rieter-Automatik. Die Polymerstränge werden beim Anfahren manuell zum Schneidkopf transportiert, bei Auftreten von Strangabrissen müssen diese Stränge wieder manuell zugeführt werden. Der Durchsatzbereich, je nach Anlagengröße wenige kg/h bis etwa 10 t/h, hängt von den Polymereigenschaften und von den Granulatmaßen ab. Diese Anlagenkonstellation erlaubt höchstmögliche Flexibilität beim Produktwechsel, z.B. in der Produktion von kleinen bis mittleren Chargen qualifizierter Compounds.
Bild 1 (links): WSG-Anlage mit Wasserbad, Strangabsaugung und Stranggranulator PRIMO Plus 100
Bild 2 (rechts): Funktionsschema einer konventionellen Stranggranulier-Anlage WSG
Unterwasser Stranggranulierung USG
Die seit mehr als 25 Jahren in der Rohstoffherstellung durch kompromisslose Zuverlässigkeit und sehr hohe Anlagendurchsätze bekannte und bewährte Unterwasser Stranggranulierung wurde durch die kürzlich vorgestellte P-USG von Rieter-Automatik im kleinen Leistungsbereich ergänzt und ist damit auch für Recycling-Anwendungen zugänglich.
Bild 3: Funktionsschema der Unterwasser Stranggranulieranlage P-USG
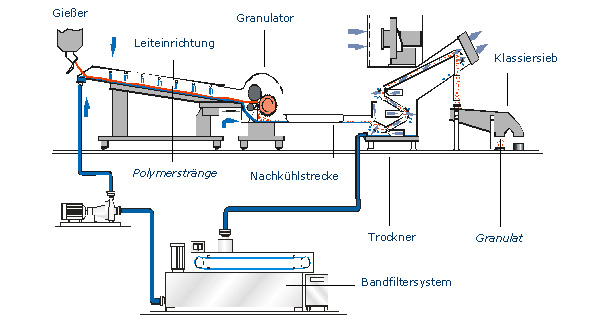
Die aus dem Stranggießer austretenden Polymerstränge werden durch eine Leiteinrichtung geführt und dort abgekühlt. Das mit den Strängen durch die Leiteinrichtung fließende Kühlwasser passiert auch den Schneidkopf.
Im Stranggranulator erfolgt der Schnitt zwischen einer feststehenden Messerleiste und dem sich drehenden Schneidrotor.
Das Granulat/Wasser-Gemisch wird in einer Nachkühlstrecke weiter gefördert, die Granulate werden dort allseitig gekühlt.
In einem am Ende der Nachkühlstrecke angeordneten Granulattrockner wird das Granulat vom Kühl- und Transportwasser abgetrennt.
Bei Arbeitsbreiten von 100, 200 oder 300 mm ist die P-USG für fast alle thermoplastischen Kunststoffe geeignet und erreicht Durchsätze bis zu 2500 kg/h (z.B. PET bottle grade).
USG-Anlagen (USG = Unterwasser-Stranggranulierung) sind automatische Stranggranulieranlagen. Die Polymerstränge werden beim Anfahren automatisch zum Schneidkopf transportiert, bei Auftreten von Strangabrissen werden die Stränge wieder automatisch eingefädelt. Daher arbeiten solche Anlagen mit reduziertem Personalbedarf, die Granulatqualität ist aufgrund des automatischen Betriebs sehr konstant, das Verfahren ist zuverlässig stabil.
Unterwasser-Heißabschlag-Granuliersystem SPHERO
Die Kernkomponente des im Frühjahr 2003 erstmalig präsentierten SPHERO Systems ist der in einem Trägerrahmen montierte Granulator. Die übrigen Systemkomponenten werden auftragsabhängig aus einem umfangreichen Baukastenkonzept zusammengestellt.
Die Funktion des SPHERO Systems wird anhand von Bild 5 erläutert:
- Die Kunststoffschmelze wird über das Anfahrventil in den Gießkopf gefördert.
- Der Schmelzestrom wird auf die ringförmig angeordneten Düsen aufgeteilt und kontinuierlich in die mit Prozesswasser durchströmte Schneidkammer gedrückt.
- Das in die Schneidkammer eintretende Polymer wird zwischen der Lochplatte und den Messern des Messerkopfes zu Granulat zerteilt, das sich durch den Kontakt mit dem Prozesswasser zunehmend verfestigt.
- Der Messerkranz wird über einen frequenzgeregelten Drehstrommotor angetrieben. Die notwendige Andrückkraft wird über eine pneumatische Verschiebung der gesamten Motorwelle aufgebracht.
- Durch den Wasserstrom wird das Granulat aus der Schneidkammer heraus gefördert und gelangt zum Trockner, wo es wieder vom Wasser getrennt wird.
- Das getrocknete Granulat wird kontinuierlich aus dem Trockner ausgetragen und an die nachfolgenden Aggregate übergeben.
- Das Prozesswasser wird gefiltert, temperiert und zur Schneidkammer zurückgeführt.
Die Abstimmung der Verfahrensschritte und Anlagenkomponenten, gegebenenfalls einschließlich weiterer kundenspezifischer Maschinen oder Anlagen, erfolgt in einer SPS-basierten Anlagensteuerung.
Bild 5: Funktionsschema des Unterwasser-Heißabschlag-Granuliersystems SPHERO
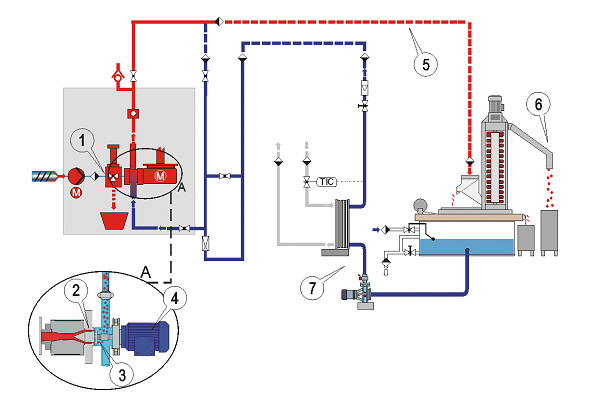
Das SPHERO Granuliersystem ist gekennzeichnet durch:
- Optimierte Strömungsverhältnisse in der Schneidkammer,
- Innovatives und ergonomisches Aufstellungskonzept durch neuartige Aufhängung aller Anlagenkomponenten in einen gemeinsamen Trägerrahmen, dadurch
- sehr gute Zugänglichkeit,
- keine Verlegung von Schienen notwendig,
- freier Zugang von allen Seiten, auch mit Hebezeug,
- schnelle Montage und Inbetriebnahme, z. B. Containerbauweise,
- Innovative Prozessführung im Wasserkreislauf, dadurch ist kein Bodenablauf nötig,
- zuverlässige Aufbereitung und Reinigung des Prozesswassers im optionalen Bandfilter,
- Bedienerfreundliches Steuerungskonzept, die wichtigsten Schalter sind redundant und können auch mit Handschuhen betätigt werden,
- Zuverlässige, materialschonende, fortschrittliche Messerandrückung; kleine Fluchtungsfehler werden über ein ausgeklügeltes System von Axialfedern ausgeglichen.
Firmenphilosophie
Die konsequent betriebene Entwicklung neuer Verfahren, Anlagen, Maschinen und Komponenten, ein kompetentes und umfangreiches Netzwerk von Niederlassungen und Vertretungen, sowie die Integration in eine starke, international operierende Gruppe, ermöglicht es der Rieter-Automatik, weltweit mit den Kunden eng zusammenzuarbeiten und ihnen immer und überall die bestmögliche Problemlösung zu bieten.
Rieter-Automatik bietet seinen Kunden kompetente und objektive Beratung bei der Lösung jeder Granulieraufgabe, weil man als Anlagenhersteller in der Lage ist, sowohl Strang- als auch Unterwasser-Granulierung anzubieten und somit die für die individuelle Anwendung optimale Lösung zu erstellen und deren Vor- und Nachteile objektiv zu bewerten. Die für den Kunden optimale Lösung wird aus einem umfassenden Baukastensystem erstellt, alle Systemkomponenten kommen aus einer Hand. Das leistungsfähige, großzügig ausgestattete Technikum kann für Grundlagenversuche und Produktentwicklungen des Kunden genutzt werden.
Schlussfolgerungen
Durch den Arbeitsschritt Granulieren wird der "minderwertige" Recycling-Kunststoff zu einem vollwertigen Rohstoff aufgewertet. Für die verfahrenstechnische Aufgabe des Granulierens stehen vielfältige Lösungsvarianten zur Verfügung, so dass für jede Anwendung eine technisch und wirtschaftlich optimierte Lösung abgeleitet werden kann. Dabei sind Planung, Beratung und Erprobung im Vorfeld der Investitionsentscheidung wichtige Voraussetzungen für den Erfolg.
Maag Automatik GmbH
Ostring 19
63762 Grossostheim, Deutschland
Tel.: +49 (0) 6026 503-100 Fax: +49 (0) 6026 503-110
Internet: www.maag.com |