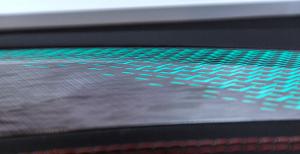
Abb.1: Dekor- und Funktionsbeschichtungen, wie sie bei Leonhard Kurz in Nürnberg/Fürth entwickelt und produziert werden, ermöglichen die effiziente Realisierung neuer Designkonzepte, hier am Beispiel einer variier- und dimmbar hinterleuchteten PKW-Türblende. - (Bild: Leonhard Kurz Stiftung & Co. KG)
Abb.1: Dekor- und Funktionsbeschichtungen, wie sie bei Leonhard Kurz in Nürnberg/Fürth entwickelt und produziert werden, ermöglichen die effiziente Realisierung neuer Designkonzepte, hier am Beispiel einer variier- und dimmbar hinterleuchteten PKW-Türblende. - (Bild: Leonhard Kurz Stiftung & Co. KG)
Das Automobil ist für viele von uns zu einer Art zweitem Wohnzimmer geworden, in dem wir tendenziell immer mehr Zeit verbringen, der Zunahme der Verkehrsdichte sei Dank. Aber anders, als dort zu entspannen, sind wir einer Reihe von Stressfaktoren ausgesetzt. Als Kompensationsmaßnahmen haben die Autohersteller in den letzten Jahren zunehmend in die Verbesserung der Ergonomie, in Assistenzsysteme, aber auch in die "Wohnlichkeit" des Fahrerumfeldes investiert, insbesondere durch die Verbesserung der Oberflächen-Umgebung. Dazu zählt das Beschichten harter Verkleidungsteile mit Softtouch-Elastomeren, das Lackieren, das Bedrucken oder die Kombination aus dekorierten Oberflächen und Struktur-teilen. Insbesondere Letzteres erweist sich durch die Fortschritte in der Folientechnik als Methode mit dem größten Innovationspotenzial, deutliche Zuwachsraten hier belegen dies.
Mehr als nur Glanz, Dekor und Kratzschutz
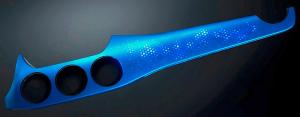
Abb. 2: PMD-Insert mit einem gedruckten kapazitiven PolyIC Sensor auf der Formteil-Innenseite kombiniert. - (Bild: Leonhard Kurz Stiftung & Co. KG)
Abb. 2: PMD-Insert mit einem gedruckten kapazitiven PolyIC Sensor auf der Formteil-Innenseite kombiniert. - (Bild: Leonhard Kurz Stiftung & Co. KG)
Bereits seit den 1980er-Jahren spielen Folien eine zunehmend wichtige Rolle für die Oberflächengestaltung von Kunststoffteilen. Zu Beginn hauptsächlich als Trägerfolien für Metallschichten zur Übertragung auf einen Kunststoffteil durch Heißprägen. Daraus abgeleitet erlangte die Folie als Transfermedium zur Übertragung von Designschichten / Druckdekors während des Spritzgießprozesses wachsende Bedeutung. Dafür wird das Rolle-zu-Rolle-Transferverfahren (IMD = In-Mold-Decoration im Transferverfahren) eingesetzt. Ein speziell von Kurz entwickeltes Folienvorschubgerät zieht die beschichtete Folienbahn (meist aus Polyester) zyklussynchron durch das offene Spritzgießwerkzeug, dabei können Endlosdesigns mittels Wegsteuerung und auch Einzelbilddekore mittels Lichtleiterpositionierung gesteuert werden. Die IMD werkzeugspezifische Klemmrahmen und Vakuumtechnik sorgt dann für eine passgenaues halten und einziehen in die Werkzeugkavität. Anschließend wird das Lacksystem "hinterspritzt" und geht dabei eine haftende Verbindung mit dem Kunststoff ein. Nach der Trennung des Folienträgers vom Lacksystem beim Werkzeugöffnungsvorgang, wird das inline dekoriert Bauteil normal entformt. Bei dieser Dekorationsmethode spricht man auch von einem "Trockenlack- Dekorationssystem" (Schutzlack inkludiert).
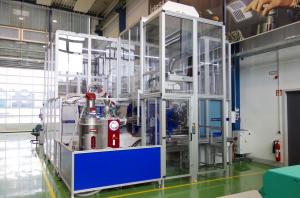
Abb. 3: Kurz hat seine Applikations- / Technologie -Versuchskapazitäten durch die Anschaffung von zwei „All-in-one“-Produktionszellen auf Basis von SmartPower-Spritzgießmaschinen mit 2.100 und 1.200 kN Schließkraft erhöht. - (Bild: Autor)
Abb. 3: Kurz hat seine Applikations- / Technologie -Versuchskapazitäten durch die Anschaffung von zwei „All-in-one“-Produktionszellen auf Basis von SmartPower-Spritzgießmaschinen mit 2.100 und 1.200 kN Schließkraft erhöht. - (Bild: Autor)
Leonhard Kurz im fränkischen Fürth ist der Marktführer bei Transferprodukten für die Oberflächengestaltung von Kunststoffteilen. Über die traditionellen Heißprägefolien und die IMD-Folien hinaus bietet Kurz ein weites Spektrum an Spezialeffekt- bzw. Funktionsdekoren an. Beispielsweise so genannte PMD (Print Mould Design)-Folienbauteile. Es sind dies glasklare Polycarbonat-Folien, die auf beiden Seiten mit einem präzise aufeinander abgestimmten Design bedruckt werden. Dadurch lassen sich Dekors mit 3D-Anmutung darstellen. Wegen der relativ hohen Steifigkeit und der hohen Erweichungstemperaturen eignen sich die PC-Folien nicht für die Direktverarbeitung auf der Spritzgießmaschine, sondern müssen außerhalb derselben durch Tiefziehen und nachfolgende Bearbeitungsschritte zu Einlegteilen konfektioniert werden. Im Spritzgießwerkzeug hinterspritzt werden daraus Armaturen- oder Mittelkonsolen für Automobile (Abb.1)
Varioform-IMD verschiebt Anwendungsgrenzen und Stückkosten
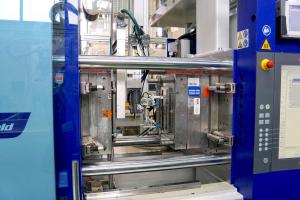
Abb. 4: Beide Spritzgießmaschinen sind mit Rolle-zu-Rolle-Folienvorschubeinheiten ausgerüstet. Die Roboter tragen eine Folien-Wärmeplatte und gegenüber davon den Sauggreifer zur Fertigteil-Entnahme. - (Bild: Autor)
Abb. 4: Beide Spritzgießmaschinen sind mit Rolle-zu-Rolle-Folienvorschubeinheiten ausgerüstet. Die Roboter tragen eine Folien-Wärmeplatte und gegenüber davon den Sauggreifer zur Fertigteil-Entnahme. - (Bild: Autor)
Das IMD-Rollendurchzugsverfahren, bei dem Polyesterfolien verarbeitet werden, als auch das PMD-Folien-Einlegeverfahren sind keine Universallösungen für Dekoraufgaben. Sie unterscheiden sich sowohl hinsichtlich der Anwendungsgrenzen als auch der Kosten. So lassen sich die von der Rolle weg verarbeiteten IMD-Polyester-Folien innerhalb eines Spritzgießzyklus nur in relativ engen Grenzen dreidimensional verstrecken.
Um einen weiteren Schritt in Richtung dreidimensionaler Designübertragung zu gehen, wurden Verfahrenskombinationen von Kurz intelligent prozesstechnisch zusammengeführt und hieraus das "Einschritt-Varioform-IMD-Rolle zu Rolle Verfahren" entwickelt.
Martin Hahn, verantwortlich für den Bereich Application, Technologie & Innovation, erläutert: "Durch diese applikationstechnische zusätzliche Technologieentwicklung eröffnet sich ein breites Spektrum in der Auswahl der Foliensysteme im Schulterschluss mit den Spritzgießsubstratmaterialien (z. B. PP, ABS-TPU). Dadurch ergeben sich neue Variationsmöglichkeiten auch im Bauteilaufbau bei gleichzeitiger Nutzung einer vielseitigen Designperspektive, sowie unter der wirtschaftlichen Betrachtung mittels einem "ONE SHOT Rolle zu Rolle IMD -Verfahren" eine noch größeren 3D-Formbarkeit zu erreichen.
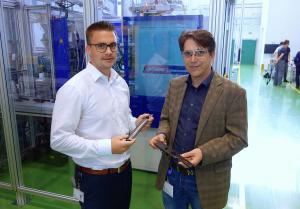
Abb. 5: Die Produktionszellen wurde von Projektleiter Fabian Bürkel, Leonhard Kurz und Marcus Otto, dem Vertriebsingenieur für Spritzgießtechnik bei Wittmann Battenfeld / Nürnberg konzipiert. - (Bild: Autor)
Abb. 5: Die Produktionszellen wurde von Projektleiter Fabian Bürkel, Leonhard Kurz und Marcus Otto, dem Vertriebsingenieur für Spritzgießtechnik bei Wittmann Battenfeld / Nürnberg konzipiert. - (Bild: Autor)
Designwechsel erfolgen analog zum Standard-IMD-Verfahren durch einfaches Austauschen der Folienrolle. Ebenso können verschiedenste Einzelbild- und Endlosdekore, sowie Funktionsfolien verarbeitet werden. Dadurch sind nun auch besonders hochwertige Oberflächengestaltungen wirtschaftlich realisierbar. IMD Varioform bildet somit ein weiteres Bindeglied in der Kurz Applikationstechnologie.
Prozesse und Applikationstechnik sind für Kurz mit entscheidend für den Erfolg. Dementsprechend wurde unser Anwendungstechnikum Spritzgießen um eine darauf ausgerichtete Versuchs- und Testanlage erweitert. Dabei haben wir uns nach einer umfassenden Kosten/Nutzen-Analyse für zwei Spritzgießzellen von Wittmann Battenfeld entschieden. Den Ausschlag dafür gab deren "All-in-one"-Konzept, d.h. dass zur Spritzgießmaschine alle Peripheriekomponenten wie Handling-Roboter, Teileförderanlage, die Materialförderung, die Werkzeugtemperiergeräte, sowie die allumfassende Reinraum-Einhausung ebenfalls aus der Wittmann Gruppe stammen und daher kompromisslos aufeinander abgestimmt und zusätzlich über die Wittmann 4.0-Softwaretools miteinander und nach außen hin vernetzt sind." (Abb.3)
Größtmögliche Seriennähe durch SmartPower-Spritzgießmaschinen
Um die Weiterentwicklung der Kurz Verfahrenstechnologien mit größtmöglicher Praxis- und Seriennähe zu betreiben, entschied sich Kurz für zwei Maschinen aus der servohydraulischen SmartPower-Reihe, konkret für eine SmartPower 210/750 (2.100 kN Schließkraft) und eine SmartPower 120/350 (1.200 kN Schließkraft), jeweils ausgerüstet mit einem Wittmann W918-Roboter und getakteten Teileförderbändern. Beide Maschinen-Schließeinheiten wurden von Kurz mit je einer Rolle-zu-Rolle-Folienvorschubeinheit ausgerüstet. (Abb.4)
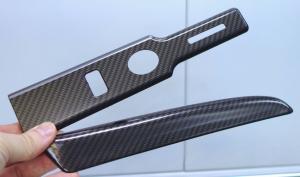
Abb. 6: Beispiele aus dem aktuellen Versuchsprogramm bei Leonhard Kurz zur Erweiterung der Tiefzieh-Verhältnisse, der Ecken- und Radienformung mit unterschiedlichen Folien. - (Bild: Autor)
Abb. 6: Beispiele aus dem aktuellen Versuchsprogramm bei Leonhard Kurz zur Erweiterung der Tiefzieh-Verhältnisse, der Ecken- und Radienformung mit unterschiedlichen Folien. - (Bild: Autor)
Die Detailkonzeption der Anlagen übernahmen Projektleiter Fabian Bürkel, Leonhard Kurz und Marcus Otto, Vertriebsingenieur für Spritzgießtechnik bei Wittmann Battenfeld / Nürnberg. Dazu Fabian Bürkel in einem Rückblick: "Uns kam es vor allem auf die Übertragbarkeit der im Versuch ermittelten Verarbeitungsparameter auf die reale Betriebspraxis potenzieller Anwender unserer Folien an. Dabei wollten wir möglichst unabhängig von variablen Einflüssen aus der Produktionsperipherie sein. Das Wittmann Battenfeld-Konzept der untereinander vernetzten und kapazitätsmäßig aufeinander abgestimmten Hilfseinrichtungen bietet uns die Möglichkeit, uns ganz auf die Abstimmung des Spritzgießprozesses mit den entsprechenden unterschiedlichsten Foliensystemen zu konzentrieren." (Abb.5)
Auf dem Sprung zu dreidimensionalen Höhen
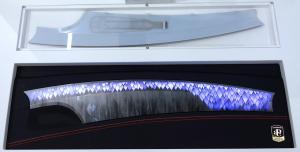
Abb. 7: Anwendung der IMD-Technik auf der Sichtseite einer PKW-Türblende. Zusätzlich ist auf der Formteil-Rückseite ein vorgefertigter Folien-Bauteil der Kurz-Gruppenfirma PolyIC mit aufgedruckter Sensorstruktur zur Integration der interaktiven Licht-Schalt- und Dimmfunktion vorhanden. - (Bild: Autor)
Abb. 7: Anwendung der IMD-Technik auf der Sichtseite einer PKW-Türblende. Zusätzlich ist auf der Formteil-Rückseite ein vorgefertigter Folien-Bauteil der Kurz-Gruppenfirma PolyIC mit aufgedruckter Sensorstruktur zur Integration der interaktiven Licht-Schalt- und Dimmfunktion vorhanden. - (Bild: Autor)
Im Fokus der neuen Versuchskapazitäten stehen die Erhöhung der dreidimensionalen Folienverstreckung (durch Infrarot-Vorwärmung und anschließendem Vakuumformen im Spritzgießwerkzeug) als integraler Verfahrensteil des Spritzgießvorganges, sowie eine systematische Optimierung der Angussposition zur Minimierung der Übertragung von Schubeinflüssen aus der Kunststoffschmelze auf die elastisch eingestellte Trägerfolie. Ein wichtiger Teilaspekt des aktuellen Entwicklungsprogramms ist die Faltenfreiheit an Formteilecken und der prozesssichere Umbugprozess für die Folie entlang des Formteil-Umrisses (Anmerkung: Als Umbugen wird das Umlegen eines Dekormaterials, z. B. einer Kunststofffolie, um eine Trägerteilkante um 90° bzw. 180° bezeichnet, mit anschließender Befestigung des umgebogenen Folienrandes auf der Trägerteilrückseite) (Abb.6).
Welches Potenzial in den Kurz Applikationsprozessen steckt, demonstriert eine preisgekrönte Anwendung für eine PKW-Tür-Innenblende (Abb.7). Dabei wurde eine partiell lichtdurchlässige Dekorfolie / IMD Einzelbildsystem mit einem gedruckten kapazitiven PolyIC Sensor auf der Formteil-Innenseite mittels IML Technik kombiniert. Beide werden innerhalb eines Spritzgießzyklus hinterspritzt. Der Sensor dient zur Touch-Bedienung der Licht-Schalt- und Dimmfunktion, mit der auch der Farbton der dahinterliegenden LED-Lichtquelle variiert werden kann (Abb.7).