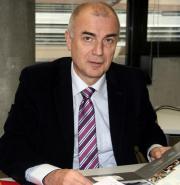
O.Univ.-Prof. Dipl.-Ing. Dr.mont. Reinhold W. Lang, Johannes Kepler University Linz, Institute of Polymeric Materials and Testing
O.Univ.-Prof. Dipl.-Ing. Dr.mont. Reinhold W. Lang, Johannes Kepler University Linz, Institute of Polymeric Materials and Testing
Prof. Dr. Reinhold Lang, Head of the ipmt, commented: "When we selected the test system for dynamic loading of plastics that best suited our requirements, one feature was particularly relevant to us: The Instron® ElectroPuls test instruments are all-electric test instruments, using patented linear-motor technology. Requiring no oil and no cooling system, the instruments support clean working conditions. There is no danger of leakage, and no need for regular oil change. The machines also excel through low-noise operation and low energy consumption. They have a small footprint and only require a simple 230V AC power supply. Further key features were the flexibility in the configuration of test methods and the exceptional response offered by the ElectroPuls controller, which enables us the precise introduction of quasi static loads as well as load or strain-controlled high-frequency cyclic loads. Last but not least, we were convinced by Instron´s expert support – Instron offers profound knowledge not only of dynamic test systems but also of their application in polymers technology.“
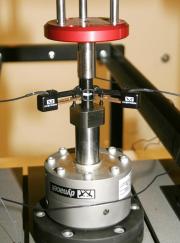
ElectroPuls E3000 testing system used for fundamental research at JKU Linz: Can dynamic loading of a notched, round specimen provide an indication of the service life of a component?
ElectroPuls E3000 testing system used for fundamental research at JKU Linz: Can dynamic loading of a notched, round specimen provide an indication of the service life of a component?
With the three Instron ElectroPuls testing systems, the ipmt is well equipped for virtually any testing task from static testing at low speeds to high-frequency dynamic tests at frequencies above 100 Hz. With a load capacity of ± 3 kN, the two E3000 systems are suitable, e.g. for static and dynamic tension and compression testing of non-reinforced thermoplastic materials. They can be set up on a laboratory table and need an installation area of no more than 0.3 m². The ElectroPuls E10000, offering a load capacity of ± 10 kN, also enables mechanical testing of high strength, high-stiffness glass and carbon fibre reinforced laminates. The Linear-Torsion Model installed at the ipmt is equipped with a patented linear motor and torsion drive, offering an angle of rotation of ±135° for biaxial testing of materials and components. Like the smaller systems, this large system is very compact and requires an area of just under 0.8 m² in the testing laboratory. In addition, the ElectroPuls E10000 used at the ipmt is fitted with a Series 3119 Instron temperature chamber, which offers a vertical test space of 660 mm and enables measurements in the temperature range from –70 °C up to +250 °C. The ipmt uses Instron® Dynacell load cells specifically adapted to high-frequency dynamic testing. In conjunction with the electronic controller, these load cells are able to compensate almost completely high acceleration forces which might otherwise distort the measurement result. Instron® Series 2620 high-precision, light-weight extensometers optimised for dynamic testing procedures enable closed-loop control.
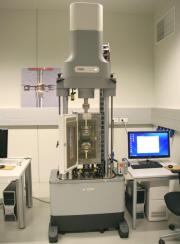
Students at JKU Linz can rely on an ElectroPuls E10000 Linear-Torsion testing system with temperature chamber for performing fracture mechanics tests on high-strength polymers. Photos: Instron
Students at JKU Linz can rely on an ElectroPuls E10000 Linear-Torsion testing system with temperature chamber for performing fracture mechanics tests on high-strength polymers. Photos: Instron
Fracture mechanics testing of plastics is a major focus of the current research projects of the ipmt. The specific objective of this fundamental research is to look for correlation between a relatively short-term, cyclic, alternating load applied in the laboratory and the durability of plastic applications under real life service conditions. Lang added: “The research at our institute, conducted in cooperation with companies in the plastics industry, focuses on the development of testing procedures, which may at some stage enable us to dispense with, or at least reduce the need for time-consuming and costly long-term studies.“ One of the Institute´s partners is its immediate neighbour, the raw material producer Borealis. Alfred Stern, Senior Vice President Innovation & Technology at Borealis, commented that Borealis relies strongly on such forward-looking partnerships: “Our approach is based on long-term, sustainable growth through innovation, and we consistently implement this approach by investing into research facilities such as the plastics institutes at JKU.“
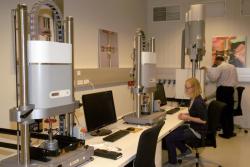
In its laboratory in the new Science Park at Johannes Kepler University (JKU) in Linz/Austria, opened in late 2011, the department of Polymer Engineering and Technologies uses three Instron ElectroPuls electrodynamic testing systems to conduct fracture mechanics studies on thermoplastic materials.
In its laboratory in the new Science Park at Johannes Kepler University (JKU) in Linz/Austria, opened in late 2011, the department of Polymer Engineering and Technologies uses three Instron ElectroPuls electrodynamic testing systems to conduct fracture mechanics studies on thermoplastic materials.
In addition to the ipmt, the department of Polymer Engineering at JKU Linz includes the In-stitute of Polymer Product Engineering (ippe, headed by Prof. Dr. Zoltan Major), the Institute of Polymer Extrusion and Building Physics (ipeb, headed by Prof. Dr. Jürgen Meithlinger), and the Institute of Polymer Injection Moulding and Process Automation (ipim, headed by Prof. Dr. Georg Steinbichler). These institutes, together with the Polymer Chemistry department at JKU, offer one of the broadest university level training programmes worldwide.
The Institute of Polymeric Materials and Testing (www.jku.at/ipmt) is one of the key institutes of the academic programmes Polymer Engineering (BSc), Polymer Science and Technologies (MSc), Management in Polymer Technologies (MSc) and Polymer Science and Technologies (PhD) at Johannes Kepler University, Linz/Austria, established in 2009. The Institute´s teaching and research responsibilities cover the fields of physics, material science, testing and applications of polymeric materials. The research profile of the institute focuses on some of the key technologies associated with the concept of Sustainable Development. It comprises research activities in the development of polymeric materials and the utilization of polymer technologies especially in the areas of water supply, renewable energies, light-weight designs for electrically driven vehicles. In addition the institute cooperates closely with partners from research and industry. Headed by Professor Lang as initiator and coordinator, the institute has contributes toward major joint research programmes.
Instron (www.instron.de) is a globally leading manufacturer of test equipment for the material and structural testing markets. A global company providing single-source convenience, Instron manufactures and services products used to test the mechanical properties and performances of various materials, components and structures in a wide array of environments. Instron systems evaluate materials ranging from the most fragile filament to advanced high-strength alloys. With the combined experience of CEAST in designing plastic testing systems, Instron enhances materials testing offerings, providing customers with comprehensive solutions for all their research, quality and service-life testing requirements. Additionally, Instron offers a broad range of service capabilities, including assistance with laboratory management, calibration expertise and customer training.