Sorting PET Flakes
Dipl.-Ing.(FH) Eckhard Zeiger, Mogensen GmbH & Co. KG
As the result of a substantial increase in the market share of PET bottles and the change in the waste streams for one-way packaging caused by the introduction of a compulsory deposit system in Germany, the quantity and composition of mixed and pre-sorted PET for recycling will change considerably. The main sales market for recycled PET is the fibre industry, but new sales markets for other high-value products, e.g. food packaging, are also opening up. In this connection, the focus is on transparent PET. This material has the largest market share and, following appropriate processing, can be reused extensively. Optical sorting systems can be used to improve the quality of recycled PET or to maintain its quality at a consistently high level. Sorting systems for PET flakes must meet very high requirements because of the sometimes only slight differences in colour and small particle size of the flakes. Specially for this application, Mogensen GmbH in Wedel has developed the MikroSort® AFO916. This paper describes the fundamentals of PET sorting, the machine engineering and one application in which PET flakes, e.g. for the foodstuffs sector, are processed with the Mogensen MikroSort®.
Introduction
To enable the supply of recycled PET flakes for high-value use in the foodstuffs or fibre industry, the recyclate must meet high standards, comparable with the specifications for primary plastic. For this reason, PET flakes are treated in different pre-sorting and downstream physical and chemical wet processes (sink and float method, hot washing and lye baths) to minimize the off -colour content, remove any packaging foils, beverage residues and other soluble impurities, and ensure compliance of the recyclate with the FDA standards to a certain extent. The content of off-colours ranges between 0.1 and max. 25 % depending on the collection system and pre-processing of the material, the content of impurities is generally below 0.1 %. After treatment by the sink and float method, the content of polyolefins and wood particles is very low. However, any metal particles, PVC and silicon report with the PET to the high-density fraction.
Following successful flake sorting, the content of colour impurities in the recyclate should only be in the region of 50-100 ppm. The "hard" impurities constitute a major obstacle to the recycling of the PET. For this reason, the content of metal, wood and extraneous plastics must be reduced to zero in theory and to the single-figure ppm range in practice.
The Mogensen MikroSort® AF 0916 presents a system with which the sorting of PET flakes in the size range 3-12 mm can be technically and economically realized (Fig.1). In the development of the new generation of machines, Mogensen is able to draw on its years of experience in machine engineering for the glass recycling and non-metallic minerals industry.
Mogensen has sold over 200 sorting machines since 1996 and is therefore a competent partner for solutions for different applications involving the sorting of bulk solids.
Sorting of Recycled PET
To allow the reuse of PET flakes in the fibre and foodstuffs industry, these must be freed of impurities such as
- other types of plastic (PVC, PP, PS, silicon),
- wood,
- metals,
- other coloured PET,
- opque PET
by various processing methods.
For the effective removal of these impurities, different detection and processing methods are employed:
- Distinction of other types of plastic in the PET with near infrared systems (NIR) by detection of the different material properties of PS, PP and PVC.
Employed in the sorting of whole bottles and, within limits, flakes from 25 mm.
- Colour sorting of whole bottles in the range of visible light.
- Distinction of impurities and off-colours for flakes in the size range 3-12 mm by sorting in the range of visible light. Depending on the application, sorting with colour-line or black-and-white cameras is possible.
- Metal detection by induction coils, removal by compressed air, sometimes integrated in existing optical detection devices.
- 5. Separation of polyolefins (bottle-tops and foil labels) by the classical sink and float method downstream of the shredder.
A comparison of the sorting methods reveals several important advantages and disadvantages:
- With whole bottle sorting in the optical range and in NIR, only a low number of pieces must be sorted (around 20-80 pieces/second). Because of the low degree of liberation, with this system on its own, it is not possible to comply with all the limit values for both the "hard" impurities and the off-colours.
- Flake sorting with the NIR system is still at the development stage and currently only works with sufficient accuracy from a flake size of 25 mm.
- In the purely optical sorting, only non-transparent impurities and metals are removed, but not different types of plastics. On the other hand, optical sorting can be used to detect differently coloured PET flakes and plastics from as small as 3.0 mm and remove these with an efficiency between 90 and 99 %.
- The sink and float process is used in many plants after shredding for the removal of polyolefins (bottle-tops or labels) and wood splinters. Together with the high-gravity PET, a high content of metal particles and entrained polyolefins also sink. This process is a necessary step in the processing of mixed PET, but separation efficiency is insufficient if this method is applied on its own.
- Metal detection with induction coils only works effectively with shredded material because a minimal, uniform distance between the metal particles and the detector is important. As these conditions are satisfied in flake sorting, this process can be combined very effectively with optical flake sorting.
Set-up and operation of the Mogensen Sorter
A vibrating feeder loosens up the material to form a single layer of particles and conveys it to a chute. On this chute, the material is accelerated, and below the edge of the chute, during free fall, or on the chute it is scanned by a high-resolution colour line camera (Fig. 2). These scanned images are evaluated by a parallel computer. Depending on the individual program settings, the results are transmitted to one or more compressed air valves, which eject the unwanted components out of the material flow.
Preconditions for sorting
For effective sorting of different materials, several preconditions must be met:
- The material allow separation of its individual particles to form a single layer.
- The materials to be separated must differ from each other in colour or lightness. Very slight differences in colour or lightness are sufficient.
- If possible, the material should be sorted in narrow particle size ranges. The sorting parameters or air pressure can then be optimized accordingly for the relevant size fraction.
What is behind the Mogensen MikroSort® AFO916
The MikroSort® AF0916 was specially developed for sorting fine, free-flowing products, such as PET flakes, rock salt, flat glass and fine stones.
The system works with a high-quality CCD colour line camera and an industrial parallel computer. With appropriate parameter settings, sorting applications in direct or incident light are possible on one machine. Particles from as small as 2.0 mm can be detected and removed in colour sorting and from 0.5 mm as dark inclusions. For certain applications, the machine can be partitioned and the material sorted onIine in two stages. Metal detection can also be integrated as an option. This enables the reliable detection of metal particles from a size of 1 mm and their removal parallel to colour detection.
Besides the detection system, the separation system was adjusted to the particular requirements for sorting fine material. To sort small particles with maximized efficiency, fast and precision-activated valves and a large number of individually actuated separation channels are necessary. A very narrow nozzle distribution in this machine guarantees a very high separation accuracy. With the use of valves that operate reliably from a pressure of just 0.5 bar, the input of compressed air into the separation zone is minimized.
In addition, the machine is equipped with a special extraction function in the separation zone. This is used to minimize any turbulence that may disturb the sorting process taking place with reject rates of up to 2.500 particles per second. Thanks to the successful adaption of the detection and separation system to the fine material, the machine operates at very high specific feed rates and with a very low oversorting rate. The compressed air consumption has been reduced substantially compared to conventional systems. To aIlow installation of the machine in existing plants, an important design criterion was the maximum compactness of the unit. So, for example, with the incorporation of a reflector box, the optical path of the camera is "folded" several times, enabling the necessary distance between the camera and the detector to be shortened.
To minimize the maintenance work, access to all relevant points in the machine is secured amongst other things by a tilting device for the components of the camera and the incident illumination unit. No special tools are required for the maintenance work. Sensitive parts such as the camera and reflector box are designed to be dust-tight and practically maintenance-free.
Application example:
Sorting of 1.6 t/h PET Flakes with 0.2 % off-colours and metal particles on one MikroSort® AF0916 with metal detection
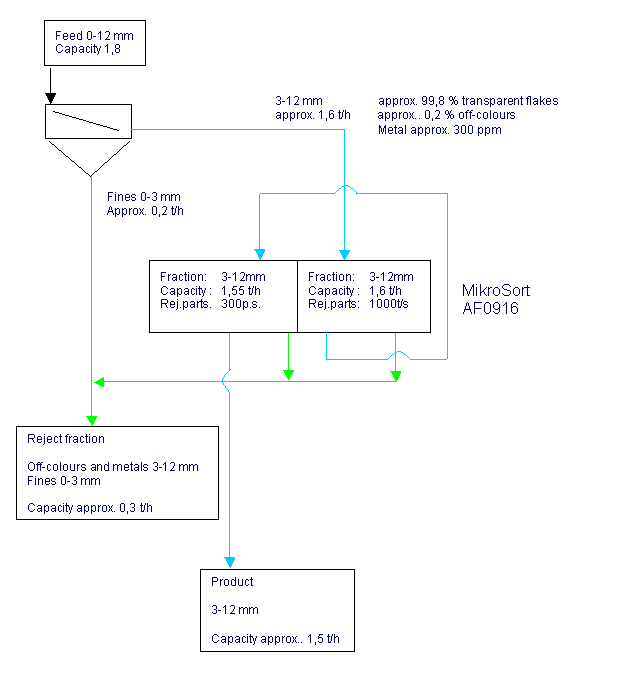
Mogensen GmbH & Co. KG
Kronskamp 126
22880 Wedel, Germany
Phone: +49 (0) 4103 8042-83
Fax: +49 (0) 4103 8042-40 Email: EZeiger@mogensen.de
Internet: www.mogensen.de |