The CreaSolv®-Process - Technical break-through in Plastic Recycling from Electro Waste
Dr. Andreas Mäurer, Fraunhofer-Institut für Verfahrenstechnik und Verpackung IVV
Every year approximately 2 million tes of electronic waste are collected in Germany. This quantity corresponds to a fully loaded train with a length of 2,000 km. One fifth of this waste is made up of plastics. These plastics cannot be re-used, because they appear as "mixed waste", contaminated with undesired flame retardants. Due to the high content of impurities and contaminants they are classified as requiring "special control" and have to be waste-handled at a high cost. This despite the fact that they represent a potentially high value resource of approximately 400 million Euros, if the contaminants could be removed.
For the first time this challenge can be resolved by a new optimized recycling process developed in co-operation by the Fraunhofer-Institute for Process Technology and Packaging IVV, Freising and the CreaCycle GmbH, Grevenbroich, Germany: The CreaSolv®-Process, protected by a patent application and a registered trademark. The CreaSolv® process is based on selective extraction of a targeted polymer from plastic waste, followed by a cleaning step. Impurities, undesired additives (e.g. flame retardants) and toxic degradation products can be separated effectively and a high purity polymer can be regained. The recycled polymers of high purity are confectioned if necessary and can meet specifications similar to virgin materials.
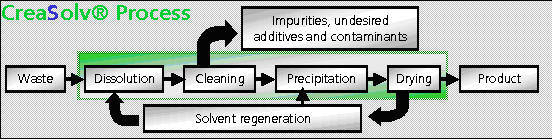
The Fraunhofer Institute has built a complete pilot plant in small scale to prove the technical feasibility and to evaluate the economics. Based on these studies the process was optimized for scale up and its profitability was confirmed. A demonstration plant with a capacity of 500 tes per year would be the logical next step. In the coming year the plan is to build the first industrial plant, aimed at accessing the large raw-material potential. This would enable companies of the electro and the waste-handling industry to fulfill the recycling quotas of the actual European Directive (WEEE - waste electrical and electronic equipment).
Recycling of Plastics from Electronic Waste?
Goals and Practical Realization.
In Germany approximately 2 million tes of electronic waste are collected annually; 400,000 tes consist of different plastic materials. Out of 59,000 tes registered plastics from the collected electro/electronic waste of the officially assigned collecting companies only 5,000 tes were processes and 54,000 tes were waste-handled [i]. With such a performance the recycling quotas of 75 to 80% as requested by the European Direction for Electronic Waste (WEEE) will not be met and the target is still too far to be met.
Several reasons are used to explain the poor performace to date, on one side the high amount of many different polymers and on the other side the possible contamination with impurities are to blame. Besides heavy metals (Pb, Cd) and PCB (old PVC-cables) flame retardants play a significant role [ii]. 78% of the flame retardants consist of brominated compounds. Investigations of the Federal Environmental Agency [iii] show that in case of fire brominated diphenylether (PBDE) for example reacts to highly toxic poly-brominated dibenzo-p-dioxines and dibenzofuranes (PBDD/F). Polybrominated biphenyls (PBB) behave similarly. Other evaluations show the building of PBDD/F already during the extrusion of polymers with flame retardants like PBDE, PBB or 1,2-bis-tribromophenoxyethane (TBPE) [ii,iv,v,vi,vii]. The toxicity of PBDD/F is equivalent to polychlorinated dibenzo-p-dioxines and dibenzofuranes and is therefore classified as "extremely high" [viii]. The German "Restriction on the Marketing and Use of Certain Dangerous Substances" (ChemVV) [ix] defines very low limits for PBDD/F: Sum 4 (1 ppb) and Sum 5 (5 ppb) and new studies prove the toxic effect of brominated flame retardants, especially of PBDE and PBB [x].
In the "Demonstration Center for product cycles" of the Fraunhofer-Gesellschaft recycling processes for plastic from electro waste have been evaluated and the new CreaSolv®-Process was developed [xi].
Separation of Dangerous Chemicals
The primer target was to develop an innovative process with integrated safe elimination of dangerous chemicals, capable of recycling fractions of plastic housing from old electro equipment.
4-Step Development Program
The realization of the process was executed in 4 Milestones:
1. Characterization of possible input materials for the process.
2. Optimization and control of the elimination of dangerous chemicals during the plastic recycling.
3. Decontamination of the separated impurities from the recycling process.
4. Concept of a complete quality control for the process.
The Four Milestones in Detail
Characterization of housing plastic fractions
For the housing samples from old electro equipment from an Electro Waste Disassembly Company a material and impurity screening was developed. Additionally samples from several shredder fractions were taken from different electro waste processes: Shredder light fractions (SLF) from different input materials (e.g. "grey" and "brown" goods) and different particle sizes.
The plastics from housings were identified with FTIR-spectroscopy and the bromine content was measured with energy dispersive X-ray fluorescence spectroscopy (RFA) in order to identify brominated flame retardants. Specific flame retardant analysis of single housings and of SLF were done with LC-MS-coupling, analysis of the SLF for PBDD/F was done with high resolution mass spectrometry. The material screening was supported by literature research.
Housing plastics: A clear dominance of ABS & HIPS plastic types could be observed and a limitation of the plastic variety to compatible styrene copolymers. This is in agreement with the research work of Riess et al. [vii]: They found a dominance of HIPS in TV-housings and ABS in monitor housings.
Impurity status: Brominated flame retardants can be found in the various mixed fractions on in per mil to percent levels. In housing plastics a higher flame retardant content was found than in mixed fractions. In general flame retardants are identified (OctaBDE, TBPE), which are known to react at extrusion temperatures to very toxic PBDD/F [vii].
Similarly critical are the analytical results of the same samples for PBDD/F. In all the analyzed samples the limitation values as outlined by the Restriction on the Marketing and Use of Certain Dangerous Substances are clearly exceeded [ix].
Conclusion
Based on these results the marketability of the mixed plastic fractions does not seem possible according to existing law in Germany without the elimination of dangerous chemicals and reduction below the specified limits.
Optimization of the Impurity Elimination
The elimination of flame retardants and PBDD/F was optimized through variations in the selection of the dissolving, cleaning and precipitation processes. For dissolving and precipitation organic solvents with a low endangering class and water were selected. The cleaning was achieved through separate process steps. From product samples for different processes were produced and granulated in order to check the physical product properties and the possible reaction to PBDD/F during the re-granulation step. The input fraction, intermediates and end-products of the different processes were analyzed for bromine, flame retardants and PBDD/F to locate the path of the impurities in the complete process. This allowed the calculation of material and impurity balances as well as elimination rates of dangerous chemicals. Those were then evaluated in relation to the impurity content data from the 1st milestone.
Process optimization: Different elimination strategies were investigated. First we tried to achieve an effective reduction of flame retardants and PBDD/F out of a plastic solution via selective extraction. With this method the contents of TBBP A (Tetrabromobisphenol A), OctaBDE and also PBDD/F could be reduced to 10-40% of the starting concentration, only minor reduction could be achieved for DecaBDE and TBPE. In following test series other processes were tested as well. In the optimized process several reduction process steps have been combined and are managed in a creative way. Below the achieved elimination rates 70-93% for brominated flame retardants and PBDD/F are illustrated in a graph. The limits of the ChemVV are not exceeded and the recycled plastics can be marketed and the characteristic material properties are similar to virgin products.
Reduction of Dangerous Chemicals
During the elimination of dangerous chemicals with the CreaSolv® Process solutions with high content of toxic PBDD/F (until ppm-levels) and Bromine (%-level) can be separated effectively. The separation of dangerous chemicals alone is not a complete concept for the recycling of housing plastics which contain flame retardants and PBDD/F, because the waste-handling cost of the separated dangerous chemicals would jeopardize the profitability of the complete process. Therefore, a detoxification or a dehalogenation of the dangerous chemicals was investigated. Tests aimed at a chemical decontamination of these solutions and a recycling of bromine were successful but not economical. As an alternative a cooperation was started for a direct injection of brominated plastic fractions into pyrolysing processes with a following flue gas wash for bromine recycling [xii].
Quality Control Concept
An analytical quality control concept was developed in parallel to process design because an insufficient separation of dangerous chemical when recycling products containing PBDD/F-would prevent the later marketing of the recycled products. Another important goal was to reduce the number of necessary expensive PBDD/F-analysis and to trace the elimination rates with alternative parameters which may be easier to measure. Additionally the equipment design of the developed analytical concepts was created as online version.
As a first step a reference substance was validated that can be controlled by simple analytical methods. For routine control of input materials and recycled polymers a cost effective online connection was developed and offers a significant reduction of the quality control cost. It is now possible to validate the PBDD/F elimination at a much lower control frequency of the PBDD/F-Analysis (e.g. 1 analysis per 50 tes).
Outlook
Based on the positive results for the elimination of dangerous chemicals a quick industrial realization of this process is intended to reach soon large scale commercialization in cooperation with industrial partners.
Literature:
- European Economic Service (2002): Recycling und Entsorgung. Ausg. v. 15.10.2002, S. 11f.
- ii. Meyer, H., Neupert, M., Pump, W., Willenbeg, B. (1993): Flammschutzmittel entscheiden über Wiederverwertbarkeit. Kunststoffe 83, 253-257.
- Hutzinger, O. (1990): Untersuchung der möglichen Freisetzung von bromierten Dibenzodioxinen und Dibenzofuranan beim Brand flammgeschützter Kunststoffe. Forschungsbericht 10403362, Universität Bayreuth. Im Auftrag des Bundesumweltministeriums
- Brenner, K.S.; Knies, H. (1990): Formation of PBDF and PBDD during Extrusion Production. Organohalogen Compounds 2.
- Hamm S.; Theisen J. (1991): Weiterführende Untersuchung zur Bildung von polybromierten Dioxinen und Furanen bei der thermischen Belastung flammgeschützter Kunststoffe und Textilien, UBA Forschungsbericht 12/91.
- Luijk, R.; Govers, HAJ.; Nellssen, L. (1992): Formation of polybrominated dibenzofurans during extrusion of high impact polystyrene/ decabromodiphenyl ether/ antimony(III) oxide. Environ. Sci. Technol. 26, 2191-2198.
- Riess, M., Ernst, T., Popp, R., Müller, B., Thoma, H., Vierle, O., Wolf, M., van Eldik, R. (2000): Analysis of flame retarded polymers and recycling materials. Chemosphere 40, 937-941.
- Weber, L.W.; Greim, H. (1997): The toxicity of brominated and mixed halogenated dibenzo-p-dioxins and dibenzofurans: an overview. Journal of Toxicology and Environmental Health, 50, p 195-215.
- Verordnung über Verbote und Beschränkungen des Inverkehrbringens gefährlicher Stoffe, Zubereitungen und Erzeugnisse nach dem Chemikaliengesetz (Chemikalienverbotsverordnung ChemVerbotsV) vom 14. Oktober 1993 (BGBl. I S. 1720), zuletzt geändert durch Artikel 3 des Zweiten Gesetzes zur Änderung des Chemikaliengesetzes vom 25. Juli 1994 (BGBl. I S. 1681).
- Böcker, R,; Kraus, V.; Schwind, B.; Pullen, S.; Tiegs, G.: Minimierung von Schadstoffen bei der Entsorgung von Verwertung von Werkstoffen der Elektronik- Toxikologische Bewertung von Flammschutzmitteln. Berichte des Bayerischen Forschungsverbundes für Abfallforschung und Reststoffverwertung. Berichtsheft 9 zum 6. Statusseminar 28. Oktober 1998
- Mäurer, A.; Schlummer, M.: Sicheres Recycling von Styrolcopolymeren aus Elektronikschrott durch Gefahrstoffelimination. In: Handbuch Umweltwissenschaften. Abfall, Entsorgung, Recycling, Umwelttechnik. Innovative Forschungen, Produkte, Verfahren und Dienstleistungen für Betriebe und Behörden, Hrsg. ALPHA Informations-GmbH, 2003.
- European Economic Service (2002): Recycling und Entsorgung. Ausg. v. 08.10.2002, S. 24.
CreaSolv® is registered trademark of the CreaCycle GmbH
Fraunhofer-Institut für Verfahrenstechnik und Verpackung IVV
Giggenhauser Str. 35
85354 Freising, Germany
Phone: +49 (0) 8161 491-0
Fax: +49 (0) 8161 491-491 Email: am@ivv.fhg.de
Internet: www.ivv.fhg.de |