 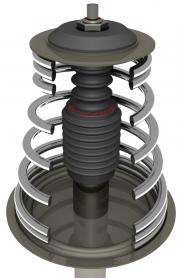 The featured jounce bumper is part of a vehicle’s shock-absorber system designed to absorb impact and dampen noise, vibration and harshness (NVH). Image: DuPont DuPont Performance Polymers is featuring an innovative automotive jounce bumper component to show how design, materials and processing can converge to deliver added performance and lower cost. The featured jounce bumper is part of a vehicle’s shock-absorber system designed to absorb impact and dampen noise, vibration and harshness (NVH).
DuPont, working with a team from Ossberger, capitalized on the flexibility attributes of DuPont™ Hytrel® thermoplastic elastomer and a unique Ossberger blow-molding technology to simplify the component from four pieces that require subassembly to a single piece. This alone significantly reduced cost, size and improved performance.
"Materials are critical in component design and the best results happen when the three primary phases in product development – design, materials and processing - converge," said Patrick Cazuc, Automotive Director Europe, DuPont Performance Polymers.
In developing this component, DuPont worked on design, using non-linear Finite Element Analysis (FEA) techniques and specialist software, as well as processing, including rapid prototyping and laboratory testing at the DuPont European Technical Centre.
These jounce bumpers made of Hytrel® have been tested by automakers on a variety of vehicles over tens of thousands of kilometres. According to an independent vehicle testing institute: "Jounce Bumpers of Hytrel® bring higher comfort and steering feedback, together with better road handling compared to PU (polyurethane) parts. Wheel rebound is also reduced with higher attenuation of low impacts. The front axis roll angle is also reduced."
Fakuma 2012, Friedrichshafen, 16.-20.10.2012, Hall B4, Stand 4201 |