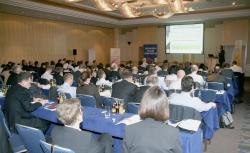 More than 100 participants attended the 6th European Nylon Symposium at the Hilton Hotel in Frankfurt am Main, Germany. The plenary presentations covered eight topics altogether over the PA manufacturing chain. At the European Nylon Symposium 2012 on February 27 and 28, 2012 in Frankfurt am Main, the organizers, the market research consultancy PCI Nylon of Bad Homburg, welcomed over 100 participants from the western and eastern European economic regions. Expert presentations were delivered on the market situation along the entire polyamide manufacturing chain, from the production of petrochemicals and the relevant intermediates in the product creation process to PA6 and PA66 applications as engineering plastics, fibers and films. Building on these presentations, round-table discussions on the second day examined future issues such as: “Biomaterials – Threat or Opportunity for PA?”, “Can the Volume of PA Continue to Grow at the Same High Price?” and “How Will PA Be Affected if Cars Become Electric?” The presenters at this one-and-a-half day event, now established Europe-wide as a polyamide expert forum, came from the global industry companies DSM Engineering Plastics, RadiciGroup Plastics, Kordsa Global, and BioAmber and from the market research companies Jacobs Consultancy, PCI Fibres, PCI Films and PCI Nylon. They examined the present situation and predicted development in the polyamide market worldwide.
Growth on the Application Side Possible
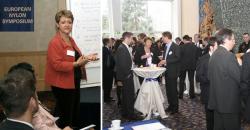 The participants used the breaks between presentations and the topic-based round-table talks on the second day of the symposium (photo: left) for intensive discussions and interchange of experience. The unanimous feeling at the event was that polyamide would certainly continue on its long successful path because of its excellent material properties, such as high strength, stiffness and toughness. However, one stumbling block could be its high price level at the moment. The present global consumption of 6.4 million tonnes in all (PA6 and PA66 together) can grow by an average 2.4% per annum over the next few years according to the current forecast. This predicted growth is, however, based primarily on the faster than average increase in demand for engineering plastics. The consequence of this is that worldwide PA consumption for fiber manufacture could drop to less than 50% of total PA production by 2020 (in Europe even to only around 30%). For the sake of comparison, in 2000 a good 70% of total global PA production still went into fiber manufacture. The main reason for the currently rising global demand is the above-average growth in Asia, especially China.
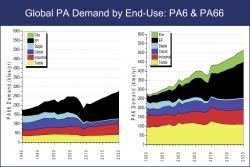 uture growth in global PA consumption (of both PA6 and PA66) is driven primarily by the continually rising demand for engineering plastics (EP). By 2020, EP’s share of consumption (including film production – “Film”) will be higher than the consumption share for the entire fiber manufacturing industry (Textile, Industrial, Carpet, Staple). Photos and charts: PCI Nylon But PA demand for fiber production will also grow slightly in the future, by almost 1% annually. This is not so much due to an increase in textile or carpet fibers. The main winner here is the industrial fiber sector, particularly for tire production. With the continuing drive for individual mobility and the current rapid rise in the number of cars worldwide resulting from this – particularly in the Asia-Pacific region – the demand for tires is also rising considerably. For 2012 alone, the estimated demand for PA66 fibers in tire production is over 300 000 tonnes, with a rising trend. Within the next 5 years, the demand for PA66 fibers in this industry will grow by a good 20%.
PA films – predominantly made from PA6 – only account for around 10% of global PA6 production. Nevertheless, they, too, will be able to hold their ground in the flexible packaging market. With properties such as excellent oxygen barrier performance, high elasticity, and good puncture penetration resistance, PA films are specially recommended as packaging for all kinds of food. The material-specific disadvantage of high water vapor permeability is overcome in film production by multilayer technology and the incorporation of suitable barrier layers. On the other hand, increased moisture penetration is an advantage in the versatile use of PA as a synthetic sausage casing. However, the packaging market is highly price-competitive, so that material price rises have a serious impact on packaging manufacturers and can often only be absorbed through intelligent “added-value” solutions.
Sustainability – Challenge and Opportunity for the Future
In the efforts of the plastics industry to improve the ecobalance of its products (including reduction of energy consumption and CO2 emissions), polyamide has played its part in the development of technically perfected solutions. A good example of this can be seen in automotive engineering. Weight-saving and metal substitution, even in the engine compartment of today’s cars, would not have been possible to the same extent without polyamides – and this trend will certainly continue. But the material cannot rely solely on this for its own eco image. This was also an issue on which the symposium focused.
All the experts agreed that the development of sustainable products and solutions will be an urgent task for all industrial companies in the coming years and decades. One aspect of this is recycling. It is already normal practice to recycle PA industrial scrap – but that alone is not sufficient. In future, recycling of post-consumer waste, too, should be increasingly integrated in a closed-loop product lifecycle (cradle to cradle recycling). A good example of this is the recycling of carpets in the USA (recovery of caprolactam from PA6 carpet fibers). With a market share of over 40%, the USA is the world’s largest carpet manufacturer, followed by Europe with around 23%. Some 5% recycled PA now flows back into US PA carpet fiber production.
Another emerging future trend is the increased use of renewable feedstocks for polyamide production. In addition to conserving resources and reducing dependency on petrochemistry, biobased plastics make a demonstrable contribution to improving the CO2 balance. Already today, for example, there are PA6.10 grades on the market produced by polycondensation of 1,6-hexamethylenediamine and sebacic acid, which contain up to 60% biobased starting materials.
One company that has declared sustainable “green” chemistry to be its sole corporate object is BioAmber Inc., headquartered in Montreal/Canada. This company has been producing bio-succinic acid on an industrial scale in Pomacle/France since January 2010 (the fermenter used has a capacity of 350 000 liters). In 2013, a production facility designed for a production capacity of up to 34 000 tonnes of bio-succinic acid and 23 000 tonnes of biobased butanediol per annum is expected to become operational in Sarnia, Ontario/Canada. Other production facilities are planned in Asia (Thailand) and on the American continent to supply the global market with biobased chemicals at prices that are intended be competitive with previous petrochemical products.
Now that C4 chemistry (succinic acid) based on renewable raw materials has been perfected on an industrial scale, the company will transfer the experience directly to the production of adipic acid (1,6-hexane diacid). With this biotechnically produced C6 building block, the way is then open to manufacture PA6 and PA66 completely from renewable feedstocks. According to BioAmber, industrial-scale production will be achieved in about 2015.
PCI Nylon is planning the next European Nylon Symposium – this will already be the seventh – for the end of February 2013, again in Frankfurt am Main. |